MI Windows is a window and door manufacturer in the United States. To improve their operations they purchased Sparklike Laser Integrated, an automated insulating glass unit (IGU) quality control (QC) technology to the production line. The deal was made together with the IG line manufacturer Glaston. In this article Operations Manager, Jake Huskins and Engineering Director, John Walsh give their insight of the market and reason why they chose to invest in Laser Integrated.
High-quality as a value proposition with window certification and standards
The current market situation has treated MI windows well. “Things have been steady” says John Walsh. However, the new Energy Star codes have created work to the production and investments have been made. For MI Windows the customer demands are related to premium quality and service. “We sell a high value product, and they expect premium quality for this value proposition, delivered on-time and complete orders.”. For this reason, purchasing Sparklike Laser Integrated served their value proposition of high-quality product which easily passes the standards for energy-efficient windows.
MI Windows takes quality seriously and wants to exceed the general requirements. They trust on certification and are FGIA and NFRC certified. Based on these, MI Windows have built their quality control process. John elaborates “QC programs follow the requirements of these programs, and then further enhanced to meet more stringent customer requirements.”
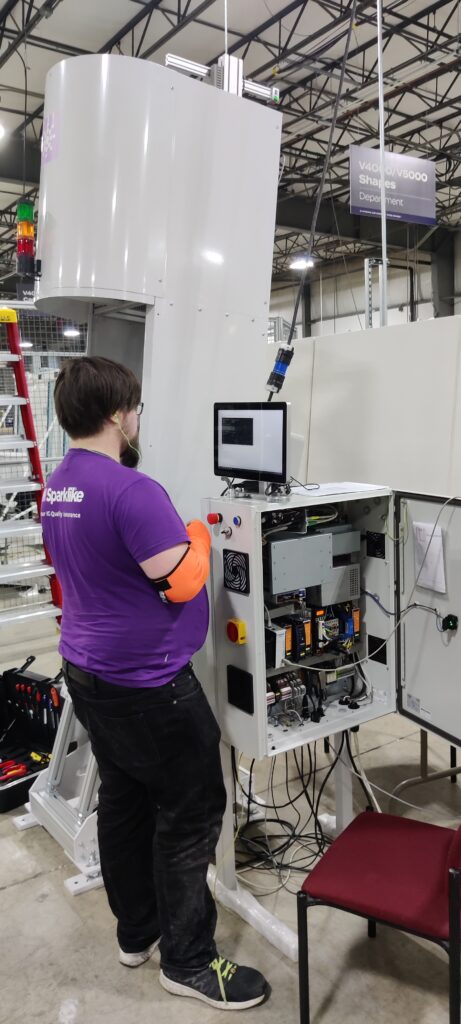
Instant result of gas level
Adding Sparklike Laser Integrated to the IG production line was not obvious at first, but once MI Windows had researched options for the new line, they saw the benefits of adding automated gas concentration system to the IG-line. They have used Sparklike Handheld to do random sampling but to enhance the quality assurance, they chose to invest in the Laser device.
“We wanted to have instant QC verification on the production line of gas fill rate. Other lines use handheld version with random sampling.”
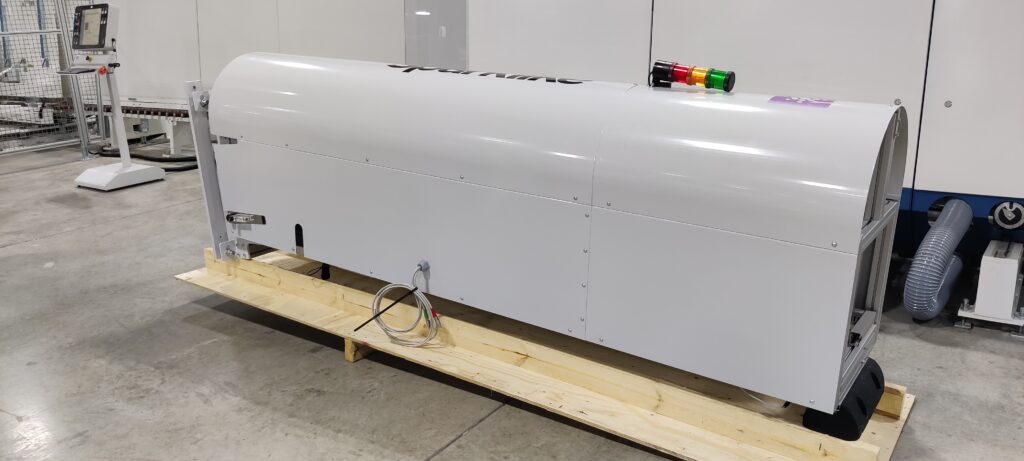
With the results from Sparklike Laser Integrated it is possible to optimize and control the gas filling process better. Also, since the quality inspection of gas levels is done to all units, the insufficient ones can be removed from the batch before sending forward. Therefore, automated IGU quality control minimize the reclaim of products.
“We expect instant results and ability to reject units before they go to window assembly lines. Eliminate sending poorly filled units to customers. Laser Integrated gives us the ability to download data for QC and maintenance monitoring and analysis.”
MI Windows asks that in the future larger sample size of quality inspections are done, if not this kind of 100 % quality assurance. They view that guidelines to measuring gas fill rate becomes more common or even mandatory than just testing random samples. With Sparklike’s product range companies within the window industry can find solutions for their quality check needs.